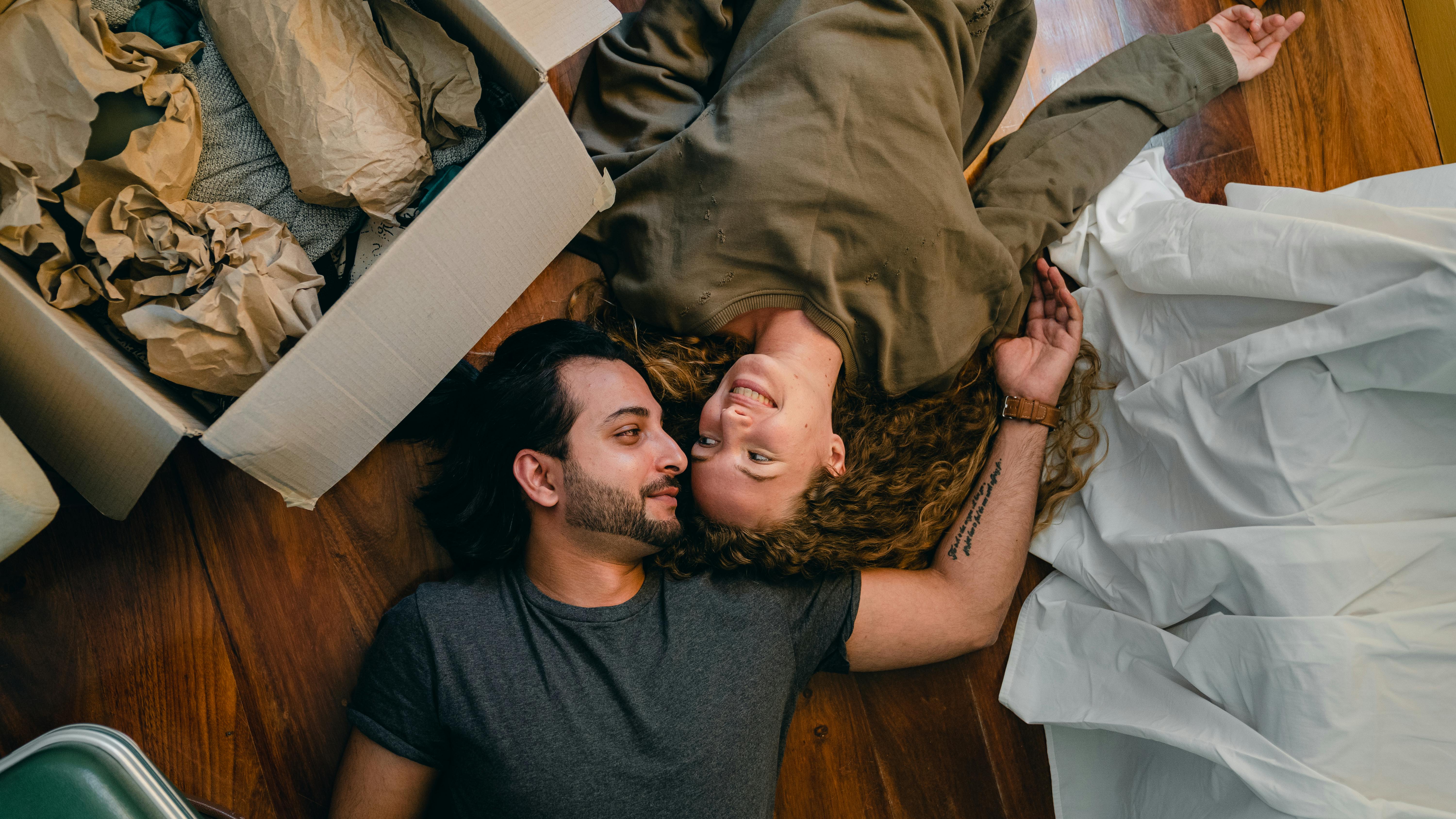
Wood Floor Board Suction Cups
admin
- 0
I have had problems with wood floorboards and wood parquet in several houses I have built. I have also identified a similar pattern with other constructors. To be totally honest, the problems I’ve experienced are largely self-made and have arisen from haste during construction or, worse, lack of experience.
Most of the older buildings have wooden floors and do not have problems with cupping. I have thought about this and have come up with a probable reason. Older buildings rarely made use of concrete slab floor construction. They are usually built using the subgrade method and have between 300mm and 1000mm of space below the supports. These structures were designed to have free air flow with vents both for the basement and for the interior of the house. This of course made them inefficient with regards to heating and cooling. The heating was often connected to a heater or a wood fire that provided heat to the occupants by radiation and convection.
Modern Australian houses are built primarily on concrete slabs. They have no ventilation and are therefore quite airtight. They are much more energy efficient. They must be, as population growth and declining resources make energy very expensive. I have noticed in houses that I have had problems with cupping of the wood floor, the floor slab was very close to the natural level of the ground. When this was combined with the natural fall of the ground towards the building, the stage was set for a small amount of water to enter, especially during severe storms and therefore problems with the wooden floor. The situation is aggravated by the structure of wooden boards or parquet blocks, which tend to have grooves at the bottom and any ingress of water at some point on the perimeter of the buildings will find its way to many parts of the floor using the grooves. like channels. like underground rivers. The bottom of the wooden floor absorbs moisture and causes it to swell, then the boards or parquet are pushed against each other, and since they are firmly attached to each other, the resulting forces cause the wooden strips to hollow out.
The solution is simple with a very small cost. However, it should be incorporated during the construction phase for maximum savings. Here is a list of the steps to follow:
-Keep the concrete slab at least 150mm above the lowest point of relatively flat sites that have not had site cuts.
-On sites that have been cut and the structure will be below natural ground level at some points, cut the site at least 1500mm beyond the construction line and keep the cut level at least 150mm below grade. of the finished concrete slab. Ensure that the ground level in the cut section is away from the building and that runoff water from the entire site flows smoothly to street level or to a suitable stormwater system.
-All retaining walls must have adequate drainage.
-Avoid site cuts that are later backfilled against a building wall. When this is done, the wall of the building is used as a retainer and a very efficient drainage system must be used. There is a possibility that the drainage system could fail over time and cause water to enter. Avoid this system except in the case of foundations, garages, basements and the like.