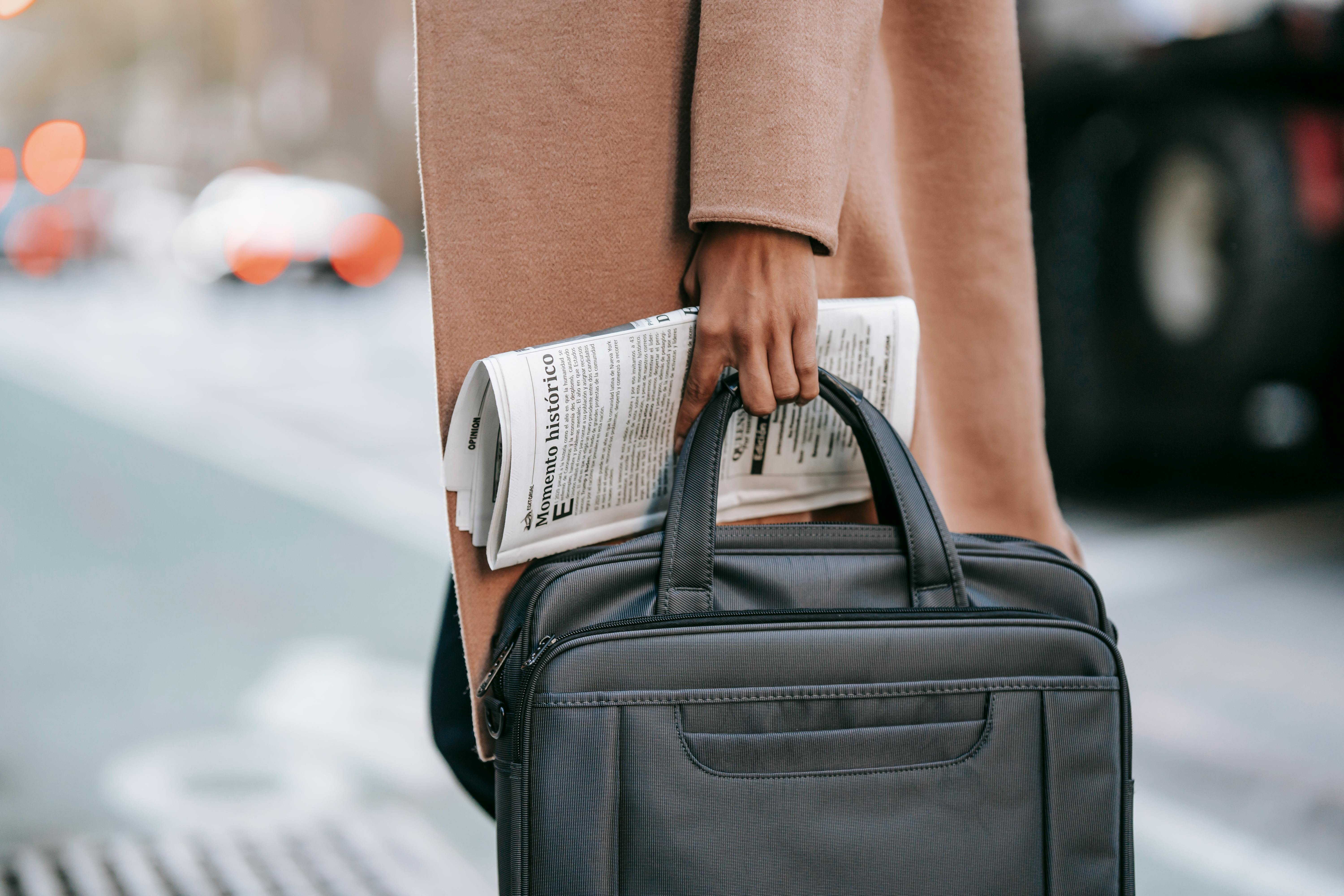
GUI time clock and its importance in direct labor cost monitoring
admin
- 0
Making the most of a manufacturer’s limited time involves a strong sense of order, as well as an awareness of the relationship between waste and productivity. This concept is especially true when considering the connection between the time an employee spends “on the clock” and the amount of work he actually does during that time. In the past, the problem of tracking employee time almost always involved the manual (paper) means by which such records were kept. However, today there is no better timing tool for clocking jobs in and out than one where the plant employee uses a graphical user interface (MISTLETOE).
Either direct labor as value in actual production, or indirect labor cost through non-productive activities of employees, working time is vital to the determination of the cost of goods sold (COGS). A virtual time and attendance workstation with a simple visual display, the easy-to-use GUI guides the plant employee when entering data associated with their ongoing job functions. By monitoring employees, work centers and/or machine production time in terms of whether it is working or not working, or on a task in one or many jobs/work orders, the GUI can maintain a continuous evaluation and in real time of productivity and work capacity of the plant.
Using simple touch screen or keyboard input, employees simply clock in and out of work directly at an online workstation. The GUI then reports a job’s start time/point, end time/point, and the work activities of both the worker and the machine between these points. The evaluation resulting from this data collection is an indicator of productivity (or lack of it) in terms of the time resource available to plant employees, in other words, direct costs. When these measures of direct labor time for a specific employee are compared to the employee’s product output for any desired date range, the GUI can calculate an efficiency rating for that employee.
With respect to indirect labor, most GUI systems also track the day of the employee’s clock in terms of time spent on non-productive activities. While these activities include specific off-the-clock break/lunch times, such events could also include indirect labor costs for legitimate on-schedule meetings or training. In either case, this employee “lost time” is spread across all shop work and included as general overhead. The GUI then calculates a total time that ought be in productive use by an employee or workplace.
Ultimately, employees come to recognize the important connection between time and productivity. With their work history documented as an indicator of productivity, employees see that their time on the clock plays an important role in the operation of the plant as a whole. Through this recognition, the GUI becomes an enterprise resource planning (or ERP) application in which employees are more fully involved in the production process. They learn how to produce better results in the shop by converting time into labor productivity and reducing COGS.