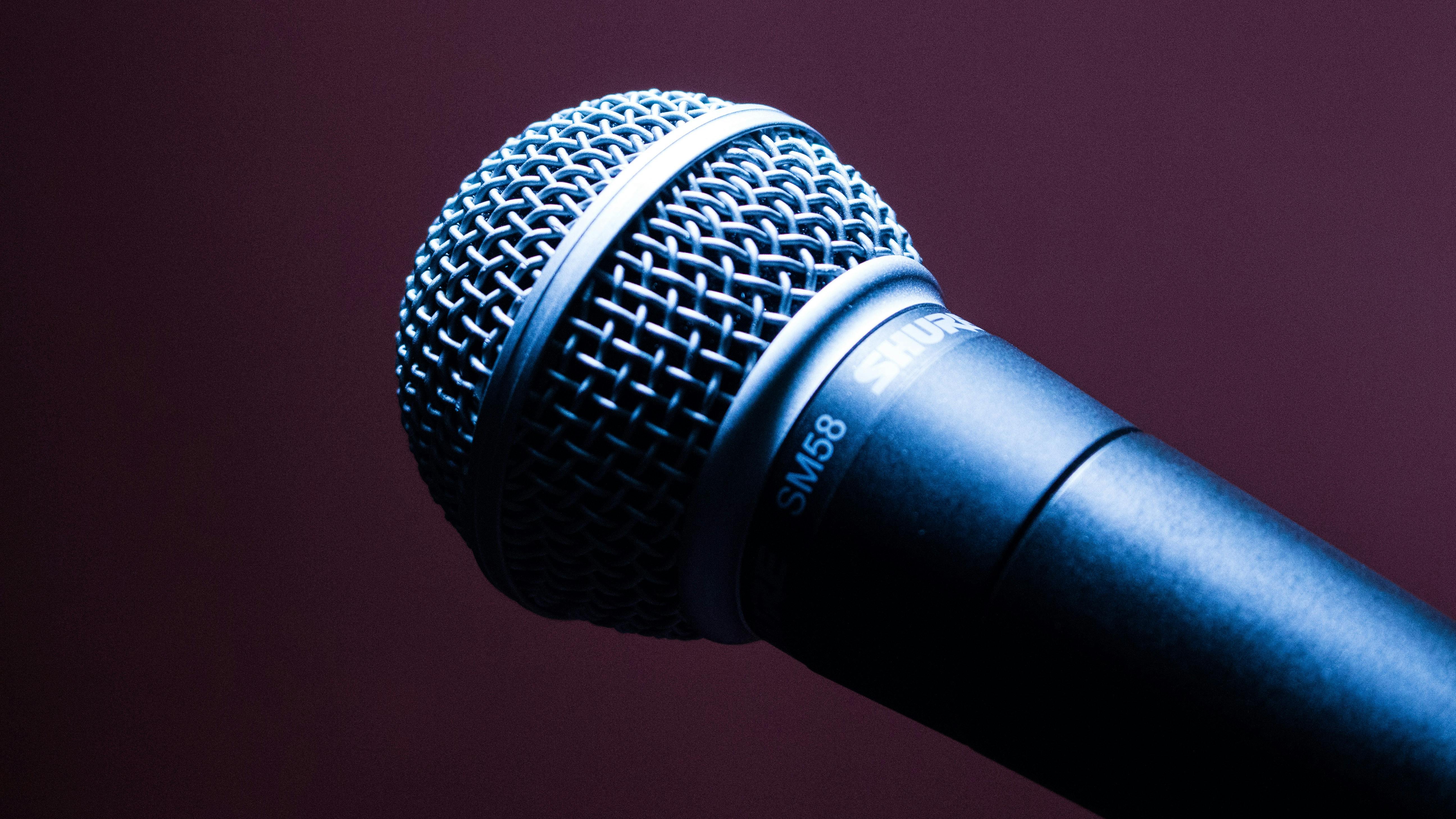
CD printing: choosing the best printing method for your project
admin
- 0
The CD printing method you choose is governed by a few key factors. These are the following:
- How many CDs do you need to print?
- What is the intended use of the final product?
- Is the budget tight for the project?
- What type of graphic material is intended for the discs? Photographic images or color blocks?
Once these factors have been considered, you can make a decision about which CD printing process is most appropriate for your particular project.
Let’s take a look at each of the processes in turn and their pros and cons.
digital CD printing
This method of printing CDs uses a printer that employs the same process as an inkjet printer that many home users will be familiar with. In fact, many home printers can be equipped with a CD print tray for use with pre-made CDRs with a printable surface. Most likely, a business that prints CDs professionally uses an inkjet printer specifically for CD printing. These printers have an autoloading mechanism that allows unattended printing of up to 200 CDs. The printer automatically loads unprinted discs and unloads finished discs onto separate spindles.
Printing digital CDs with one of these printers is slow, but there are no fixed setup costs. This is fine if the number of discs in the order is less than 100, or 200 if there is no fixed imminent deadline for the order.
This printing method is capable of producing very professional looking CDs, as an inkjet printer can print at very high resolutions. However, the printed surface needs protection and a clear lacquer coating should be applied to the discs to prevent moisture from coming into contact with the ink through handling or exposure to humid environments. This need significantly increases the total time of the project. There are printable discs available that have a specially formulated surface that becomes waterproof after printing, but they are more expensive than regular printable discs, so a decision should be made based on the urgency of the project; Extra expense for waterproof discs or extra time for the application of a clear coat?
CD screen printing
CD screen printing is ideal for artistic designs that involve solid areas of color. Screen printing is done using a rotating bed machine that has 5 separate stations where a different ink color can be applied. CDs can have a base color first applied over the entire area of the disc, which means that a screen printed CD design can consist of a total of 6 different colors at most.
The ink used in the CD screen printing process is sensitive to ultraviolet rays, and since each color is applied at one station, the disc is moved under an ultraviolet lamp as it rotates to the next station. The UV lamp cures the ink and this only requires a moment of exposure.
As the name of the process suggests, screen printing is applied through the use of very fine mesh screens. There is a separate screen for each color in the artwork design. To create a screen, a film is produced that has the areas where ink should not be applied to the disc darkened. The new screen is initially coated with a thermal emulsion. Film and screen are aligned on top of each other by guide marks and placed in an exposure unit. When the screen is exposed to bright hot light, the area of thermal emulsion that is not protected by the dark area of the film cures. The screen is then washed with a water spray and the uncured emulsion areas are washed away to reveal the mesh.
The screen is then fixed on your station. Once all the screens have been prepared in this way, printing can begin. CDs are loaded into the machine by an automated robotic arm system. They are placed on a platen that holds the disc firmly in position. At each station, ink is added to the top of the mesh screen and a squeegee goes over the top pressing the mesh down onto the disc surface and forcing the ink through the fine holes in the mesh into the surface of the disk. The ink stroke lasts approximately one second and each station inks one disc simultaneously as soon as the first 5 discs have entered the system. This speed means that a screen printing machine can print over 3,500 discs in an hour, so large orders can be completed quickly.
However, there are significant fixed installation costs due to the need for screens and film. These can be reduced by limiting artwork to fewer colours, with a single color print on a silver disc being the most cost effective print. Fixed costs mean that this CD printing process is only really viable for orders of more than 100 discs.
The CD screen printing process is capable of producing a truly amazing CD print at very high resolution due to the use of extremely fine mesh screens. However, it is not ideal for printing photographic images due to the presence of subtle color gradients in these images. What makes the screen printing process really unique is the availability of fluorescent and metallic inks that can really add a WOW factor to your CD print.
CD lithographic (offset) printing
This printing process is very different from the screen printing process and the two printing machines are set up very differently. The lithographic process takes advantage of the fact that printing ink and water do not mix as much as oil and water.
The image of the artwork is applied to a CD lithographic printing plate using a laser. The printing plate surface has a rough texture and is pre-coated with a thermally reactive emulsion.
Printing plates are treated with chemicals to allow removal of the exposed area of thermal emulsion from the printing plate. Once the printing plate has been prepared, the area containing the artwork image becomes receptive to ink and repellent to water. The areas of the CD build plate that should not be printed attract water but not ink. The printing plates are then assembled on a rotating cylinder in the lithographic printer.
As the printing plate goes through each rotation, it passes over a set of rollers that apply water to the plate, the water is drawn to the rough surface, where no ink should be applied to the disc.
The printing plate then passes over rollers as ink is added. The ink is attracted to the smooth areas of the printing plate. A cylinder wrapped in a rubber blanket then rolls over the plate and collects the ink. The CD design image is then transferred from the rubber blanket cylinder to the CD, which is held securely in a metal platen. Again, this process is very fast, as many parts of the process occur simultaneously and many discs are printed together.
The ink used is UV sensitive like for screen printing, so when the discs are exposed to UV light they cure immediately.
Lithographic printing is perfect for printing photographic images, as it can handle areas with subtle color gradients very well. However, it is not as good for large areas of solid color, as there may be a discrepancy in ink coverage which can result in a “ragged” print on the CD.
As with CD screen printing, lithographic printing has a fixed setup cost, regardless, in this case, of how many colors are involved in printing. It only becomes economically viable for print runs of 100 discs or more and the more discs that are printed, the lower the unit cost.
CD printing Illustration points to check
It is very important to present the highest resolution image possible to your provider. The better the quality of the image, the better the quality of the final product. Be sure to check that all images, especially photographic ones, are in their original format. It is not enough to transfer a low resolution 100 dpi image to a file template created at 300 dpi. The original image will not print well and you will be disappointed with the result.
Check that dark photographic images print well by making test prints before committing to production. If the image is to be screen printed, providing the supplier with a pantone reference code for each of the colors in the design will ensure that the print will look exactly as you expected. If you already have a printed disc and are looking for a repeat, ask your supplier about the color scheme. Most vendors will provide this service, giving you peace of mind that the final product will remain consistent with previous projects.
Summary
To summarize the above information according to the intended end use of your CDs:
- If you only need a short run of less than 100 discs, digital printing will be the most cost-effective CD printing method. Certainly, there is no compromise on print quality, but there are no fixed setup costs.
- If the image you want to print is based on a photograph, lithographic printing is the way to go.
- If your image consists of 1 or more solid color areas, then screen printing is the CD printing method of choice for a sharp result. Fluorescent and metallic artworks also require screen printing.